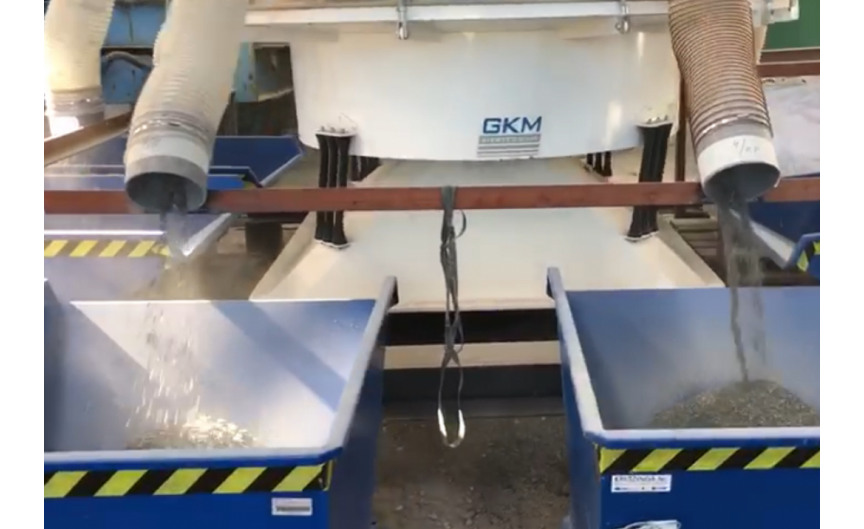
2019/8/9 - Van sloop naar prefab
Beton recyclen is niet nieuw, maar de wijze waarop Circulair Mineraal het aanpakt wel. Zij streeft naar upcycling. Het beton dat zij terugwint met de CM-breker is zo zuiver van samenstelling dat het gebruikt kan worden als grondstof voor hoogwaardige toepassingen.
De eerste praktijkproef heeft inmiddels plaatsgevonden. Beton dat bij de sloop van het IBM Datacenter in Middenmeer vrijkwam, wordt door Spaansen in Harlingen verwerkt tot prefab gevelelementen.Achter Circulair Mineraal gaan zes Nederlandse sloop- en recyclingbedrijven schuil.
Zij zetten zich in om hun industrie nog circulairder te maken. Uit het beton dat zij bewerken wordt 100 procent van de grondstoffen teruggewonnen, ook de fracties kleiner dan 4 millimeter! De man die de sloopbedrijven samenbracht is Dick Eerland. “Als we beton echt circulair kunnen maken dan heeft dat een enorme impact op het verduurzamen van de economie. Het is de meest gebruikte bouwstof. Niet alleen in Nederland, maar wereldwijd. Door de CO2-uitstoot van beton – 1 kg CO2 per kilo cement – te verminderen is er veel duurzaamheidswinst te behalen”, weet hij.
Hoogwaardig
Met lede ogen zag Eerland aan dat teruggewonnen beton bijna uitsluitend diende als onderlaag voor wegen. “Het is goed funderingsmateriaal, maar een groot deel van de waarde gaat verloren. Feitelijk blijft het ‘downcycling’. Wij streven naar ‘upcycling’ en willen de grondstoffen die vrijkomen bij sloop zo lang mogelijk in de keten houden. Daarvoor ontwikkelden we een nieuwe installatie. Deze stelt ons in staat om kwalitatief hoogwaardige grondstoffen te winnen die geschikt zijn voor de productie van nieuwe betonproducten, zoals rioleringsbuizen of prefab bouwelementen. De gevelelementen – met korrels tot 16 mm – die Spaansen gebruikt van de reststromen van het IBM-gebouw zijn daar een voorbeeld van.”
Constante kwaliteit
Om herwonnen beton hoogwaardig te kunnen inzetten, is het van belang dat het product een constante kwaliteit heeft. Eerland: “Op zich is dat niet nieuw. Ook betongranulaat uit conventionele puinbrekers moet voldoen aan zuiverheidseisen. Er mogen geen bestanddelen als zand, metalen, hout of kunststoffen in zitten.” Maar, wat is dan het verschil tussen hun breker en andere puinbrekers? “Wat de CM-breker onderscheidt is dat hij betongranulaat verwerkt tot zand, grind en cementsteenpoeder. Dit doen we met een geavanceerde bewerkingstechniek; een speciaal procedé waarbij de kleine brokken elkaar onder druk ‘schoonschuren’; het cement schuurt van de korrels af. Zand en grind krijgen zo een 80 procent schoon oppervlak en zijn daardoor geschikt als toeslagmateriaal voor nieuw beton. Het cementsteenpoeder dat we winnen kan als vulstof ingezet worden door de betonindustrie voor de productie van zelfverdichtend beton.”
De cijfers
Eerland verduidelijkt de winst die behaald wordt aan de hand van cijfers. “Anderen maken van ‘sloopbeton’ korrels. Deze zijn 4 tot 30 mm groot. Maar dat is slechts de helft van het beton dat vrijkomt bij sloop. De andere helft – bestaande uit fracties tot 4 mm en zand – wordt meestal ingezet in de wegenbouw en verdwijnt uit de grondstofcirkel van de betonindustrie. Doordat wij al het vrijgekomen beton verwerken en aanleveren aan de betonverwerkende industrie kunnen we de maximale milieuwinst behalen.” En niet alleen door het proces. “De CM-breker is een mobiele installatie, die we naar de slooplocatie brengen. We verwerken het beton dus in de buurt en beperken daardoor ook de transportkosten en CO2-uitstoot door vervoersbewegingen tot een minimum.”
Meer capaciteit
De belangstelling voor de nieuwe techniek is groot, blijkt als Eerland verder praat. “Op dit moment verbouwen we de installatie zodat we grotere volumes kunnen verwerken. De eerste CM-breker kon 20 ton per uur verwerken, na de revisie hopen we een capaciteit te hebben van 30 ton per uur.”,